Palin Sludge Consolidator
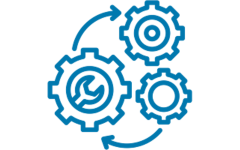
Built to run without the need for maintenance
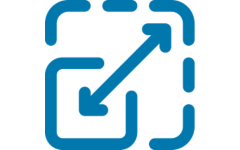
Each Palin is designed and built to customer specs
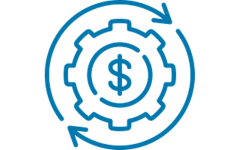
Cost effective alternative to competing technologies
Sludge-laden water collected from a recirculation tank is continuously sent to the Palin Sludge Consolidator, which performs the core function of a vertical DAF system—consolidating and removing floating industrial sludge.
The Palin system utilizes a MASCon (micro-aeration system) to introduce fine air bubbles that enhance solids flotation—similar to the dissolved air flotation principle. These bubbles attach to rising paint particles, aiding in their separation and removal. As these particles coagulate into a sludge mat, they are scraped from the surface and directed into a dewatering system like a bag or sludge dryer.
The Palin System is a fully customizable unit designed to each of our clients needs.
Models typically come in standard widths of:
32″
48″
54″
66″
84″
The width is representative of the size of the scraper used in the Palin System.
The length of the system varies depending on the specific application, chemical program, and retention time needed.
To complement our Sludge Consolidator Systems we offer numerous adders that enhance the Palin System’s user interface.
- Platforms
- Stairs
- Ladders
- Stainless Steel tank
- Dewatering bag carts
- With sump
- Without sump
- Controls architecture
Download Literature
Leading Companies Using a Palin Sludge Consolidator
All product and company names are trademarks™ or registered® trademarks of their respective holders. Use of them does not imply any affiliation with or endorsement by them.
Frequently Asked Questions (FAQ's)
Answer:
The Palin Sludge Consolidator offers numerous advantages over competing centrifuge technologies. A few key differences in design and performance are listed below:
- Palin: Zero maintenance or downtime required.
- Centrifuge: System bearings need to be rebuilt frequently and a rotating assembly maintenance.
- Palin: Custom controls can communicate with a wide variety of plant PLCs (Programmable Logic Controllers).
- Centrifuge: Standardized equipment where one size tries to fit all applications
- Palin: Less than 50 PPM of solids returned to the process.
- Centrifuge: Returns several thousand (2,000 – 10,000 PPM) solids back to the process water.
- Palin: Can handle significantly larger volumes at a higher rate.
- Centrifuge: Limited effectiveness when handling large volumes.
- Palin: Adds retention time to the system, creating a larger hydraulic footprint, facilitating easier management of de-tack chemicals.
- Centrifuge: Does not contribute to retention time or hydraulic footprint in the same way.
- Palin: Designed specifically for each individual system, considering both hydraulic and solid loading characteristics.
- Centrifuge: Standardized equipment where one size tries to fit all applications